Our management of water consumption and efficiency is just one part of our ongoing commitment to collectively find new and creative ways to tackle the global challenges we face in a thoughtful and impact-focused way.
We strive to create extracts and ingredients people love, in a way that protects people, and our planet.
Our new UK headquarters was designed and constructed with sustainability very much in mind.
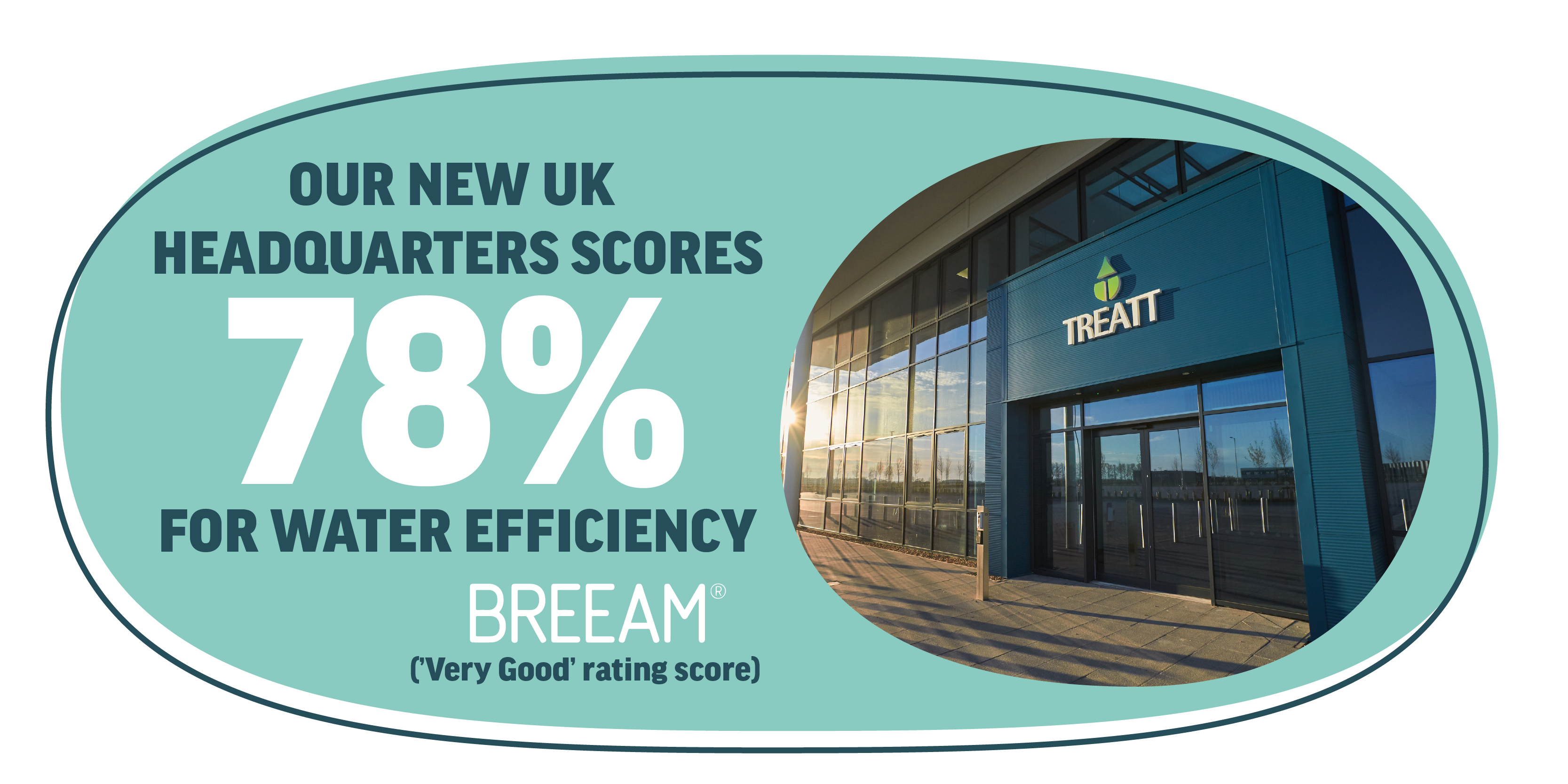
Here are a few of the ways we are making sure every drop counts.
1. Surface and storm water is recycled
All surface and storm water is retained in a large aquifer system - a geological feature that sits under the site acting as a containment system. Up to 900,000 litres of water can infiltrate the aquifer and be extracted as drinking water 400 days later. Storm water retention on site also includes a 20% allowance for climate change.
2. No irrigation needed
Our landscape and management plan incorporates native species that require no irrigation. As well as this, having close monitoring devices such as automatic leak detection on our water main and our water system, keeps our business management system current, sustainable and effective through regular safety tour inspections.
3. Water saving features
To minimise our water consumption in different parts of the building, we use washbasin mixer taps with self-closing push buttons, toilets fitted with dual flush water-saving valves, urinals are fitted with cistermiser flow control, and in our production areas knee operated sinks are fitted with a 12-15 second turn-off water saving feature.
4. Our clean-in-place process
To enhance our cleaning process water savings, we have installed a clean-in-place (CIP) system for our blending tanks. The CIP system allows us to automatically clean our blending tanks after each batch. The system will pump hot water and detergent to and from tanks. Each tank is fitted internally with a sophisticated sprayball which directs flow and enables the tanks to be cleaned quickly and with less water and detergent. The waste water from the CIP is pumped to the DAF (waste water treatment) plant which separates the oil from the waste water. The final rinse of the tanks from the CIP unit is harvested and used as the first rinse for the next tank clean, thereby saving water overall.
Our sustainability journey across the globe
Over the last 12 months, we have made significant investments in our internal infrastructure that will make a big difference to the sustainability journey we are on. We are working with a team of highly experienced consultants who have aided in the development and implementation of a global sustainability strategy. We have also recruited dedicated resources to help further our progress.
As well as the water management initiatives in the UK, we are currently looking at a water efficiency and wastewater management systems at our operations in the US. This will enable us to monitor water usage during processing and manufacturing at our locations across the globe in the near future.